About the Company
KRN Heat Exchanger and Refrigeration Limited (KRN) specializes in manufacturing fin and tube-type heat exchangers for the HVAC&R industry. Utilizing non-ferrous metals such as copper and aluminum, the company produces various products, including condenser coils, evaporator units, evaporator coils, header/copper components, fluid and steam coils, and sheet metal parts.
KRN offers heat exchangers in diverse shapes and sizes, with tube diameters ranging from 5mm to 15.88mm, designed to meet specific client needs and adhere to industry standards. Over the years, KRN has strategically expanded its operations by enhancing its manufacturing capabilities and product offerings, as evidenced by its investment in state-of-the-art facilities and advanced testing methodologies, such as helium leak testing and salt spray testing, to ensure the highest quality standards.
Promoter Insights:
- Anju Devi is the promoter and whole-time director, having provided consultancy services at LLOYD Electric. She has been with KRN Heat Exchangers since its founding in 2017.
- Santosh Kumar Yadav is the promoter, CEO, chairman, and managing director with over 19 years of experience in manufacturing heat exchangers and refrigeration units. He previously headed operations at LLOYD Electric and has been with the company since its inception.
Business Overview
Products Portfolio:
1. Evaporator Coils
Evaporator coils are a key component in cooling systems such as air conditioners, rooftop units, fan coils, dryers & more. Their primary function is to absorb indoor heat and transfer it to the refrigerant flowing through copper tubing. The fins on these coils significantly increase the surface area, enhancing heat exchange between the refrigerant and air. As air passes over the evaporator coil, it gets cooled, and this cooled air is circulated back into the room, maintaining the desired indoor temperature. The refrigerant absorbs the heat, transforms into gas, and then moves to the compressor and condenser coil to release the absorbed heat. Regular maintenance of these coils ensures efficient cooling and energy efficiency.
2. Condenser Coils
Condenser coils are vital in HVAC and refrigeration systems for heat dissipation. Their role is to release heat from the system into the surrounding air, usually outdoors. As refrigerant in the system changes from vapor to liquid, the heat energy is released during the condensation process. The design of condenser coils, especially those with bent configurations and end plates, maximizes surface area and improves heat transfer. These coils help condensing units and chillers achieve efficient cooling with reduced energy consumption. Their compact and space-saving design makes them suitable for a variety of applications, from home air conditioners to industrial cooling systems.
3. Fluid and Steam Coils
Fluid coils are commonly used in HVAC systems to heat or cool air inside buildings. They are essential for maintaining comfortable temperatures in controlled environments, such as office buildings and industrial processes. These coils work by transferring heat between air or water, ensuring energy efficiency. Steam coils, on the other hand, are used in industrial applications like power generation plants and food processing. They transfer heat from steam to air, raising the air's temperature, or from chilled water to cool the air, making them essential for precise temperature control and energy efficiency in various industries.
4. Condensing and Air-cooling Units
The company specializes in custom manufacturing condensing and air-cooling units that meet the specific needs of its customers. A condensing unit consists of a compressor, condenser coil, and fan motor, all connected through pipelines and housed within a durable casing. These units are controlled through a panel to ensure precise operation. The company’s ability to custom-manufacture these units in various sizes and designs gives them a competitive edge. These units are integral to refrigeration systems, ensuring effective cooling for a wide range of applications.
5. Headers / Copper Parts
Headers are important components in HVAC systems that distribute the refrigerant evenly across the system’s tubes. The company uses advanced machines such as CNC tube benders and CNC flute punching machines to produce headers with precision. CNC technology ensures that these parts are produced with exact dimensions and minimal imperfections, contributing to the overall efficiency and performance of HVAC systems.
6. Sheet Metal Parts
As a manufacturer of sheet metal components, the company produces parts like end plates for evaporator and condenser coils, as well as other custom-designed sheet metal parts used in HVAC systems. They use advanced machinery, including hydraulic machines and CNC punching machines, to produce precise and customized metal parts. This ability to manufacture both standard and custom parts allows the company to meet the specific needs of its clients. The precision of CNC punching machines ensures high-quality production and enables the company to serve a broader market with tailored solutions.

Raw material supply chain
Company operates as a fully integrated manufacturing unit, transforming raw materials into finished heat exchangers. By maintaining strong supplier relationships, it ensures a consistent supply of raw materials, helping to control costs, quality, and supply stability, which provides a competitive edge. The company sources most of its raw materials through imports, mainly from Malaysia, South Korea, Thailand, Vietnam, and China, accounting for over 79% of total purchases.
Manufacturing Facilities:
Company operates two manufacturing units in Neemrana, Rajasthan, with a total installed capacity of 566,551 units for evaporator and condenser coils, 618,667 units for headers/copper parts, and 556,800 units for sheet metal parts. In FY24, the company achieved over 84% capacity utilization.
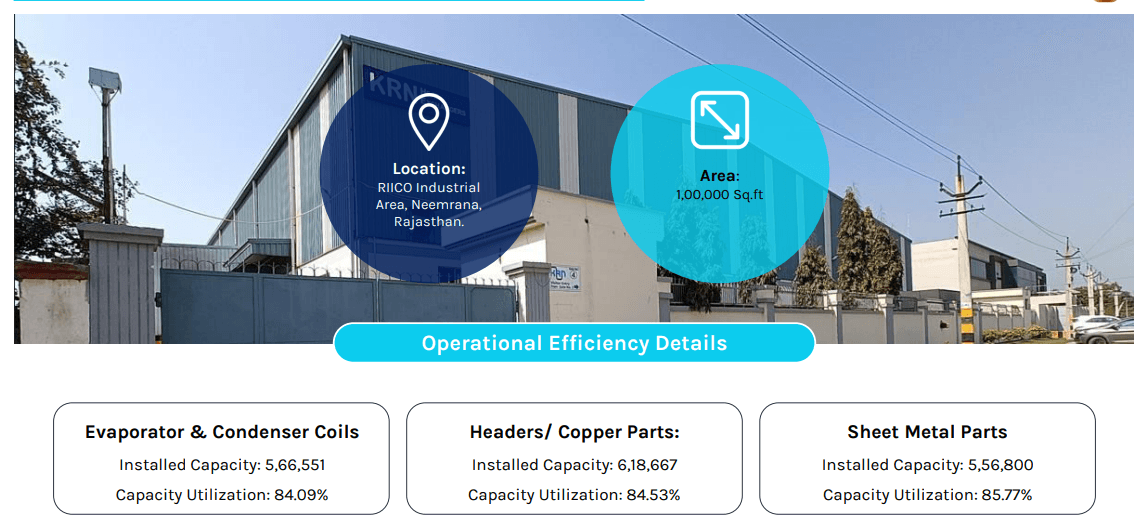
Manufactuirng Process:
Company manufacturing process of heat exchangers involves several meticulous steps to ensure efficiency and reliability. It begins with Component Fabrication, where tubes, shells, and fins are produced using extrusion, rolling, and stamping techniques. These components are then assembled into the final configuration with precise alignment and fit. Welding and Brazing techniques are employed to create robust, leak-proof connections. In the Testing and Quality Assurance phase, hydrostatic or pneumatic pressure tests verify structural integrity, while helium leak detection ensures the absence of leaks, and performance testing confirms thermal efficiency. During Finishing and Shipping Preparation, surface treatments are applied to enhance durability, followed by a thorough final inspection to meet all quality standards before packaging. Finally, in the Transportation and On-Site Inspections stage, the heat exchangers are securely shipped and inspected post-installation to confirm proper functionality.
Product & Usage Scenarios:
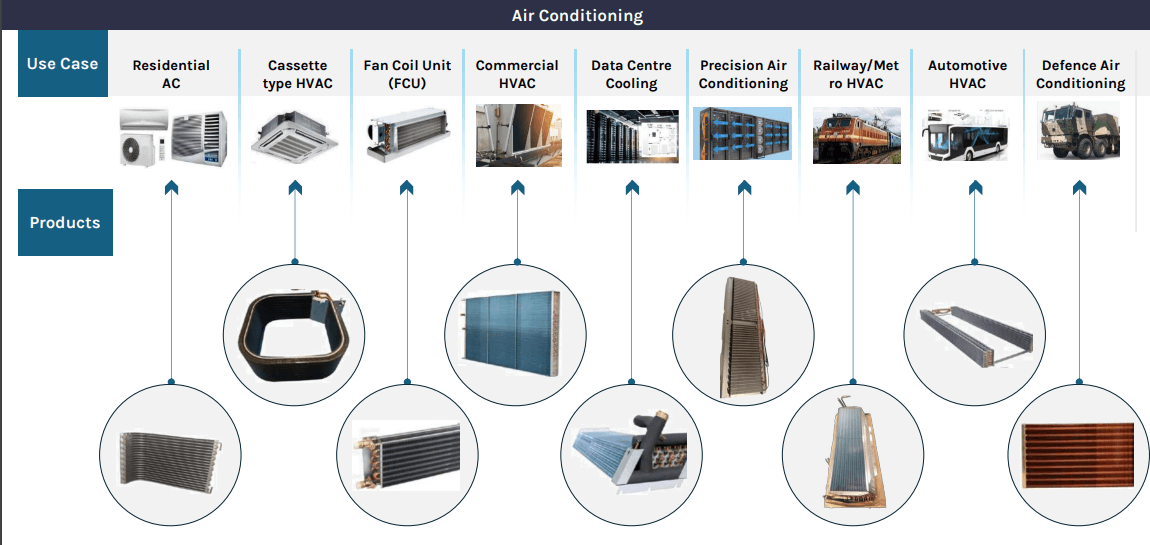
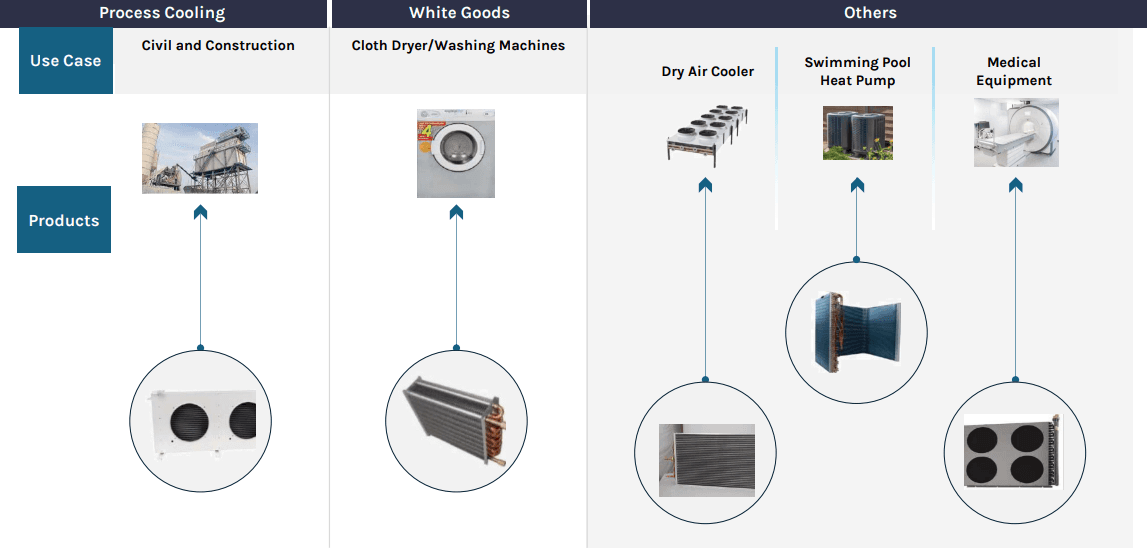
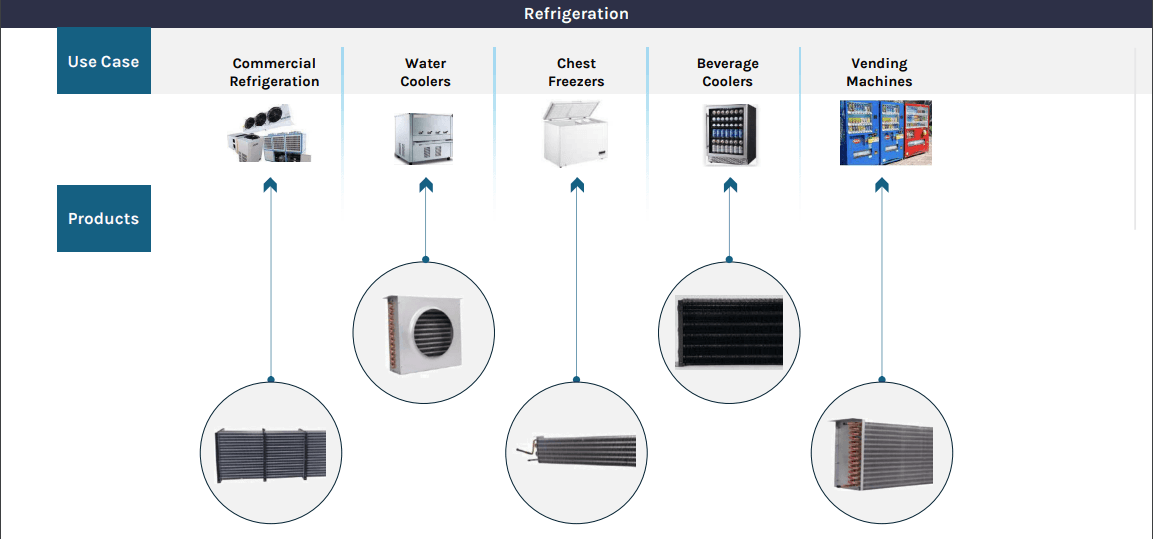
New Arrivals:
Company offers innovative solutions, including the Bar & Plate Heat Exchanger, which efficiently transfers heat between fluids without direct contact using fine, grooved metallic plates for optimal thermal diffusion and safety. The company also provides Oil Cooling Units with blowers and motors, designed to regulate oil temperature, enhancing engine and transmission performance through effective heat dissipation. Additionally, its Roll-Bond Evaporators deliver versatile design flexibility for direct cooling refrigeration systems, ensuring efficient thermal performance tailored to diverse applications.
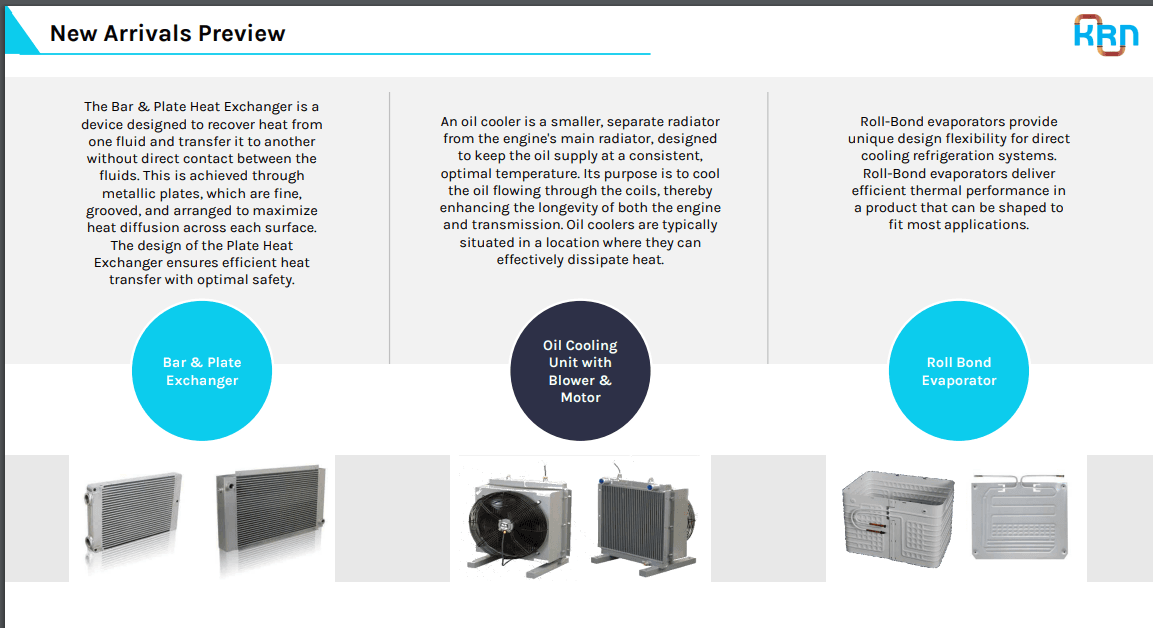
Clientele:
These products serve essential roles in air conditioning, heating, ventilation, refrigeration, and process cooling. KRN ensures product longevity and corrosion resistance with advanced nano and powder coatings. Known for quality and innovation, KRN partners with leading industry players like Daikin, Schneider Electric, and Blue Star, while strategically expanding its global reach and enhancing operational efficiency.
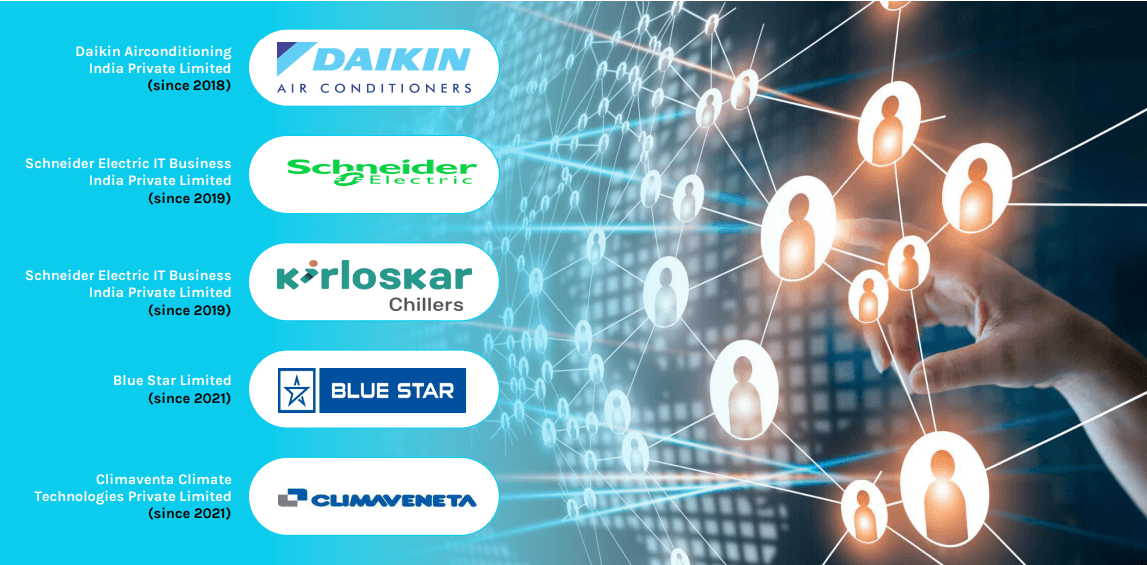
Geographical Wise Revenue Breakup FY24:
Domestic Sales
- Rajasthan: 41.24%
- Maharashtra: 11.04%
- Karnataka: 9.44%
- Haryana: 8.53%
- Uttarakhand: 3.81%
- Himachal Pradesh: 3.54%
- Gujarat: 2.50%
- Uttar Pradesh: 1.52%
- Diu Daman & Dadra Nagar: 1.32%
- Others: 2%
Exports:
- United Arab Emirates: 8.39%
- USA: 3.45%
- Italy: 2.34%
Revenue Bifurcation - Product wise
- Condenser Coils: 55.24%
- Evaporator Coils: 37.49%
- Other Operating Revenue: 5.70%
- Headers/ Copper Parts: 1.52%
- Sheet Metal Parts: 0.05%
Upgrade to Capsule+ now to unlock exclusive content!
₹990% OFF
₹99/YEAR